India’s electric vehicle (EV) market is burning rubber. Annual sales hit 1.67 million units in FY24, a jump of nearly 42% from FY23 (data from the Vahan dashboard, minus Telangana). This is a strong sign that EVs are taking off. Currently, EVs only make up about 7% of total automobile sales, but it is expected to cross 45% by 2030. This growth will be driven by two-wheelers (moped and scooters) and three-wheeler/four-wheeler commercials vehicles. In fact, two-wheelers already rule the roost, making up over 55% of EV sales, followed by three-wheelers (almost 40%) and four-wheelers (a measly 5%). Official estimates predict a whopping 45.5% compounded annual growth rate (CAGR) for the sector until 2030.
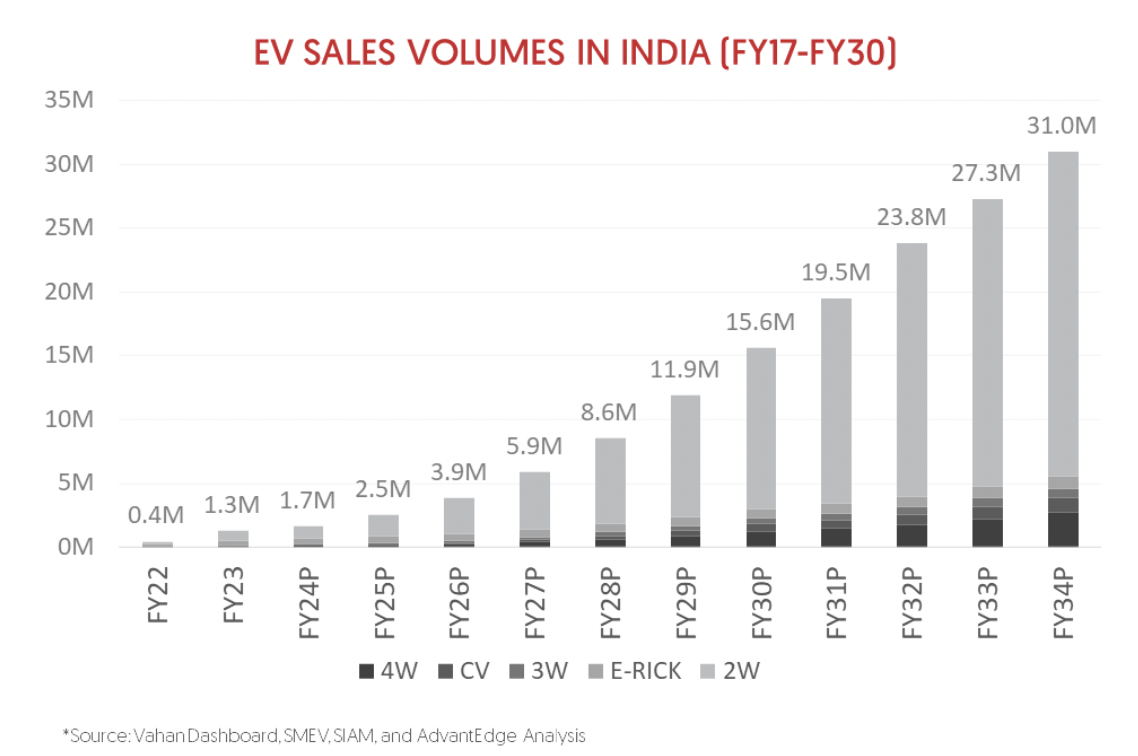
India’s EV boom is fuelled by critical EV component imports, mostly from China, right now. But with technological advancements and the government’s policies like the production linked incentive (PLI) scheme for Advanced Chemistry Cell (ACC) Battery storage and auto/auto-components, announced earlier, and the E-Vehicle Policy, announced last month, there is a clear path to reducing reliance on imports of parts and building a self-sufficient EV future.
Why are imports so big?
The heart of an automobile is its powertrain. Compared with vehicles with internal combustion engines (ICE), EV powertrains have 60% fewer components. It consists of batteries and the battery management system, electric motors with controllers, inverters and rare earth elements. These make up at least 50-60% of any EV and the majority of this component ecosystem is not yet established in India.
For example, India currently lacks domestic production capacity for lithium carbonate equivalent (LCE), a key battery precursor, crucial for lithium-ion batteries, the core technology powering EVs. Similarly, electric motors and their controllers, which manage power delivery, require specialized technology, manufacturing processes and scale that India currently lacks. Magnets within these motors often rely on rare earth elements, some of which are not available in India. Due to these reasons, India’s nascent EV ecosystem relies heavily on imports from China, which is a major supplier of these EV components not just for India, but for manufacturers worldwide. China has 75% of the world’s battery production capacity and more than 50% of global EV production and exports. It accounted for nearly 30% of India’s auto component import bill of Rs 20.3 billion in FY23.
India’s heavy reliance on imported EV components makes its manufacturers vulnerable to disruptions in the global supply chain, which can stem from many factors, including trade disputes, wars, geopolitical tensions, production slowdowns, and even pandemics. A prime example is the semiconductor shortage that plagued the world between 2020 and 2023. This shortage, impacting over 150 countries, led to significant price increases for consumer electronics. Economists termed the crisis a “perfect storm”, caused by a confluence of events like the COVID-19 outbreak, the US-China trade dispute, and Russia’s invasion of Ukraine. The chip shortage forced EV manufacturers to scale back operations and, in some cases, temporarily halt assembly lines.
There are enough reasons for developing strong local supply chains for EVs in India. But it won’t be easy. While manufacturers in major cities have shown some success through value addition on certain components, this hasn’t been replicated outside these urban centers. To understand this disparity better, let’s examine the hurdles faced by domestic manufacturers.
The challenges of local manufacturing
Manufacturing cutting-edge battery cells, electric motors, and power electronics requires specialized knowledge and experience. Currently, established foreign players dominate these technologies, making it difficult for Indian companies to compete. Compounding this challenge is India’s limited research and development (R&D) in the EV sector. Globally, the top 5 cell manufacturers dominate the supply chain and invest billions of dollars into R&D, developing new and improved cell chemistries. Unfortunately, R&D spending in this area in India is still ramping up, putting domestic manufacturers at a major disadvantage compared with their foreign counterparts.
Setting up large-scale production facilities for EV components requires significant upfront investment. This can be a major deterrent for domestic companies, especially compared with established foreign players who benefit from economies of scale. Limited access to raw materials further complicates the situation as India lacks a strong domestic supply chain for critical resources like lithium, cobalt, and nickel. For example, while India has some battery pack assembly facilities, large-scale cell manufacturing capabilities are limited, due to a lack of knowledge in advanced cell chemistry and the high cost of setting up such facilities. The same situation applies to electric motors. Though some manufacturers can produce basic electric motors, advanced, high-performance motors for EVs are often imported due to technological limitations.
The good news? Lithium-ion battery prices are dropping, making EVs more affordable, which can accelerate the shift towards electric mobility. For manufacturers, lower battery costs can lead to higher profit margins, encouraging further investment in EV development and production. But there is a flipside too. Lower battery costs may discourage domestic battery production in the short term, as established players in China may continue to offer lower prices due to economies of scale.
Policy push
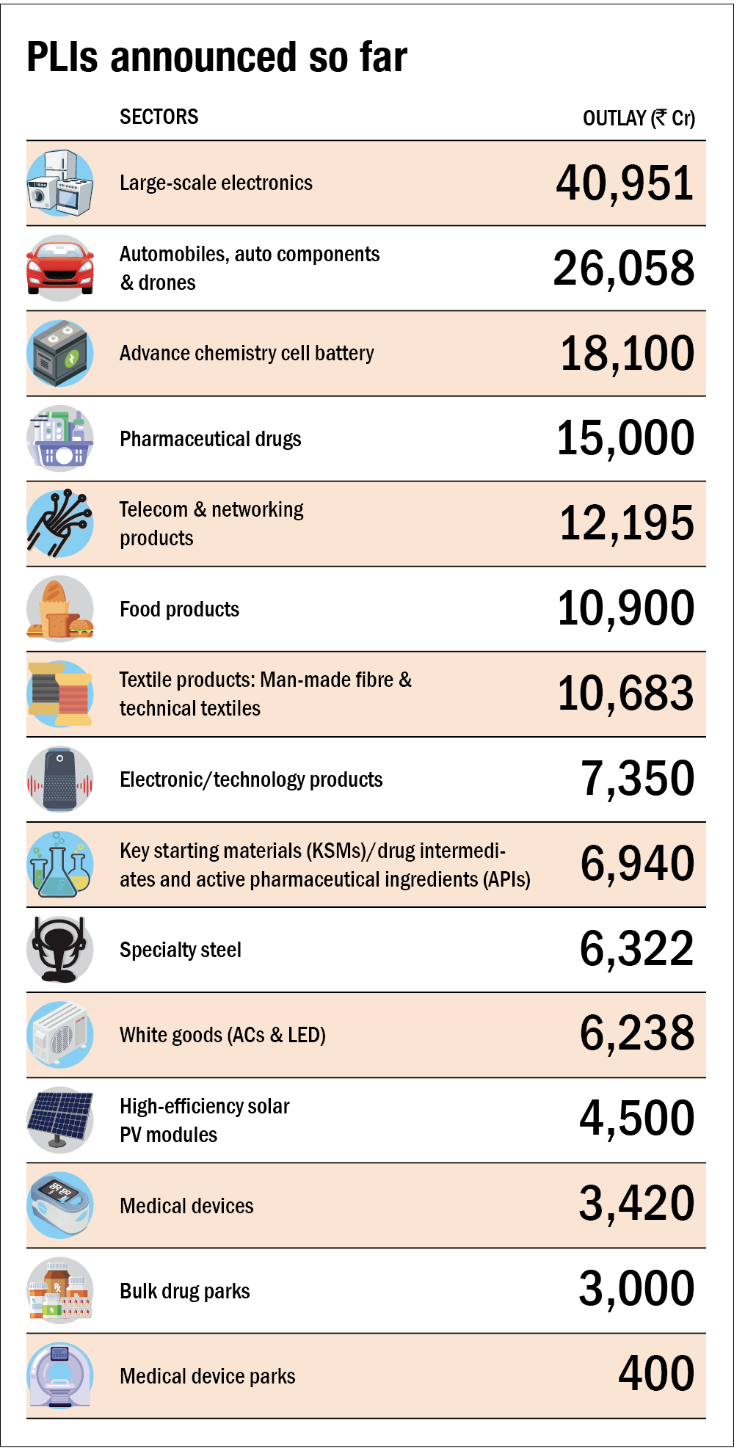
Policy intervention, therefore, becomes critical in boosting domestic EV production. Government policies and incentives play a crucial role in creating a level playing field for domestic manufacturers, thereby promoting local manufacturing. Policy support for R&D can accelerate technological advancements and innovation, helping Indian companies compete globally. The central government has already been instrumental in driving the adoption of green mobility.
For example, in 2013, the Ministry of Heavy Industries & Public Enterprises launched the National Electric Mobility Mission Plan (NEMMP) 2020. This ambitious plan aimed to achieve annual sales of 6-7 million hybrid and electric vehicles by 2020, from less than 50,000 then. Additionally, the government launched the Faster Adoption and Manufacturing of (Hybrid &) Electric Vehicles (FAME India) scheme in 2015 to encourage both the production and use of electric vehicles. FAME India provides subsidies to both manufacturers and consumers, reducing the upfront cost of EVs and making them more attractive to buyers, thereby stimulating demand. The government spent nearly Rs 900 crore in the first phase alone. In the second phase (FAME II), which started in April 2019, the center put aside Rs 10,000 crore for the scheme.
Further initiatives include the PLI scheme for the automotive industry. With an allocation exceeding Rs 25,000 crore, the PLI scheme incentivizes domestic manufacturers of critical EV components like batteries, electric motors, and power electronics. The cabinet approved a separate PLI Scheme for the National Programme on ACC Battery Storage. This program aims to achieve a manufacturing capacity of 50 GigaWatt hours (GWh) of ACC batteries with an outlay of Rs 18,100 crore.
The government has further demonstrated its commitment to EVs by reducing the Goods and Services Tax (GST) on EVs from 12% to 5%. Additionally, GST on chargers and charging stations has been reduced from 18% to 5%.
What else can be done?
While existing incentives have jump started the domestic EV manufacturing ecosystem, more comprehensive policies and incentives are needed to address lingering challenges. One crucial area is workforce development. The government can provide more support for skilling and training programs, creating a workforce with the necessary expertise for EV production. It could also facilitate technology transfer and collaboration between domestic and international players.
A simplified and transparent regulatory framework is also essential. This would reduce bureaucratic red tape and attract further investment. Financial incentives could take the form of increased financial support, additional tax breaks, and investment incentives for establishing EV manufacturing facilities and R&D centers.
The government has already announced an allocation of Rs 2,671.33 crore for a FAME III scheme in the Interim budget this year, but details are yet to be released. Government funding is a crucial piece of the puzzle, but private investment also plays a key role. Data from Tracxn shows that the sector received commitments for $1.2 billion in funding between January-August 2023, compared with $1.9 billion recorded in all of 2022. This increased investor interest coincides with legacy automakers finally embracing EVs. Companies like Mahindra and Mahindra, Tata Motors, and even new players like Ather Energy and Ola Electric are investing heavily in developing their own EV technologies. The government’s recent budget allocation of Rs 1 lakh crore to support R&D and innovation in new-age sectors, including EVs, can significantly boost domestic technology development.
We also need more research on various aspects of EV technology, including battery chemistry, energy storage systems, vehicle dynamics, and smart grid integration. The good thing is that there is a renewed focus on EVs at universities and research institutions. Collaborations between academia, industry, and government bodies will only foster innovation and knowledge exchange.
Battery manufacturing is the key
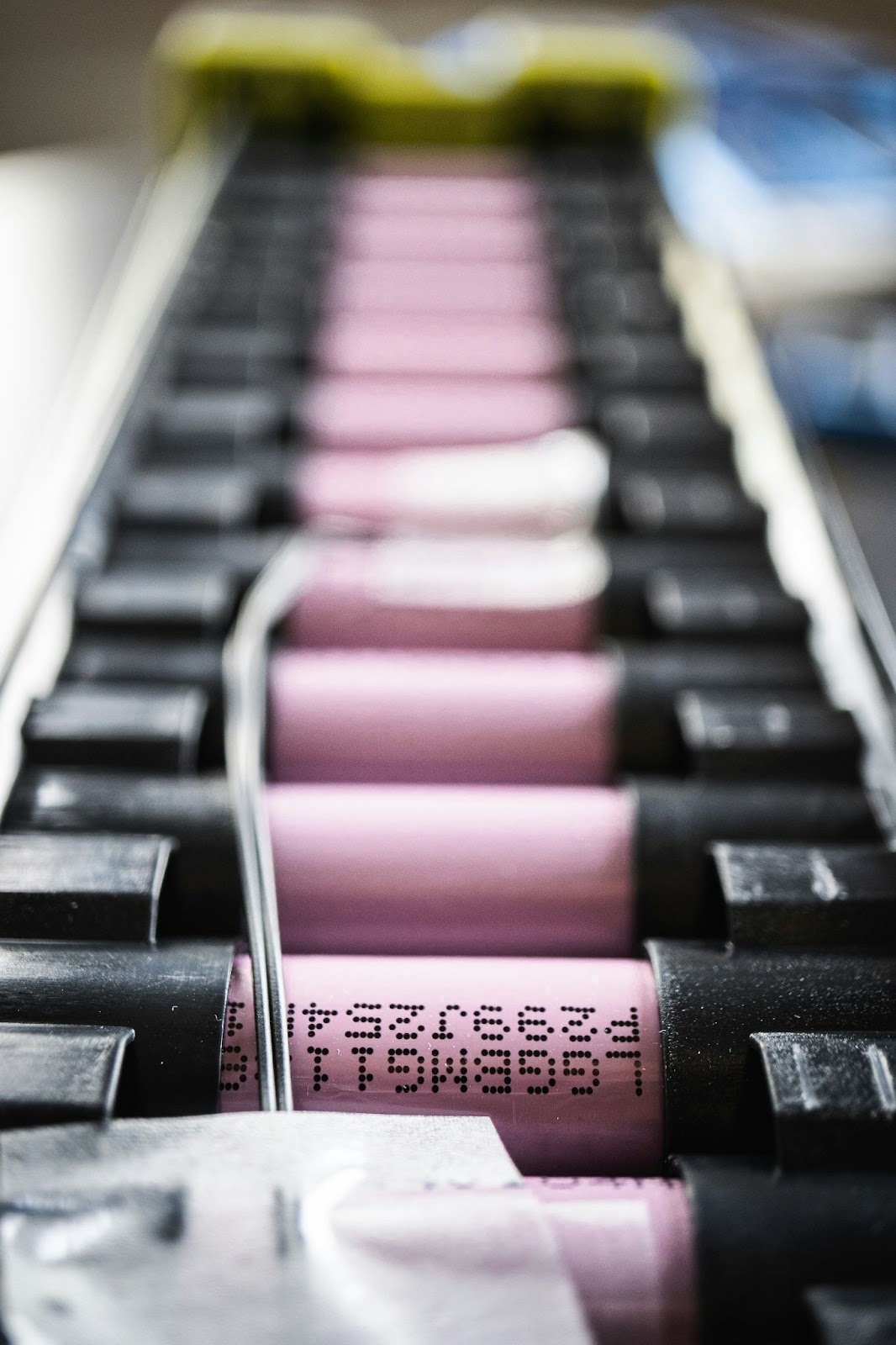
The key, however, is battery manufacturing, and companies have realized it. Major players such as Reliance Industries, Mahindra & Mahindra, and Tata Motors are all investing in Giga factories for large-scale battery production. Even startups like Ola Electric and Ather Energy are working on battery tech, focusing on innovation and catering to specific vehicle segments. Then there are players like Exponent Energy, working on 15 minute fast charging. A handful of companies are working on different parts of the battery puzzle and it has made investors sit up and take notice. They are also looking beyond electric two- and three-wheelers, recognizing the potential of the entire EV ecosystem. A new class of investors has emerged, which is focused on energy transition and sustainability themes including funds like AdvantEdge Founders, Micelio Fund and Avaana Capital.
The road ahead
Success hinges on reducing domestic manufacturers’ reliance on imported components. By implementing a combination of supportive policies, fostering innovation, and encouraging private sector investments, India can build a robust domestic EV ecosystem and become a leader in the global clean mobility revolution.
Beyond reducing emissions, a thriving EV industry can significantly boost economic growth. This includes lowering the oil import bill, attracting investments, promoting innovation, and creating new export opportunities. India’s EV sector is on the path to becoming a $206 billion market by 2030, according to a study by the Centre for Energy Finance (CEEW-CEF). This growth is projected to create 10 million direct and 50 million indirect jobs.
The Niti Aayog has projected a promising future for EV financing, with a potential market value of $50 billion by 2030. However, this transformation requires a collective effort from policymakers, industry stakeholders, and investors. All parties must work towards a shared vision of a sustainable and self-reliant electric future for India.
The road ahead is long, and there may be challenges along the way. However, with the right approach, India can march forward with its domestic EV ambitions, leaving its import dependence behind.